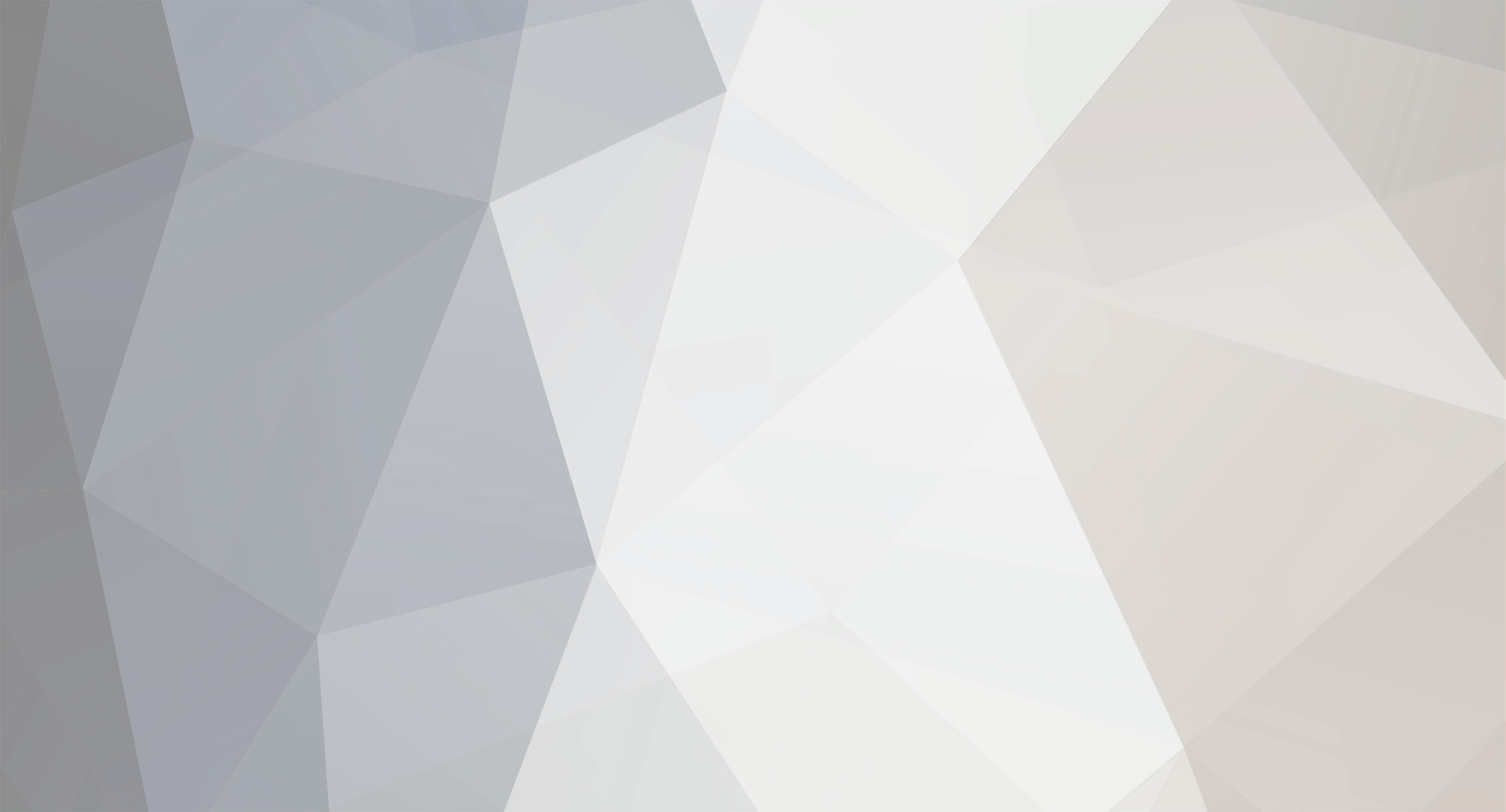
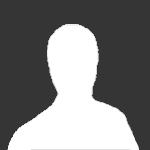
log1call
General Member-
Posts
493 -
Joined
-
Last visited
-
Days Won
1
Content Type
Profiles
Forums
Events
Store
Everything posted by log1call
-
I've seen in the bottom of their five and their twenty litre bottles and there is what looks like brass, steel and water contamination... lots of it sometimes. If you buy it often, take a look in the bottom of the containers and report back if you like. I don't buy it but I know someone that buys lots for his vintage engine and car collection and he goes through heaps of it... the amount of s*** in the barrels is staggering.
-
Isn't it better to have thin bearing material on the steel backing though? Thick layers of "whitemetal", can and do squeeze out under pressure... which was a major disadvantage of the old poured bearings. It used to be that race/high performance bearings had thinner than usual "whitemetal". Perhaps things have changed since I was a young fellah?
-
Mate... do not buy Elf oil... have you looked into the bottom of a bottle of that stuff? I have seen and heard of water, brass and steel sediment in the bottom of their oil packs... Buy one of the old established oils.. not jusy some johnny-come-lately that sponsers a race car with their shit product.. that doesn't mean anything. I have seen guys tip the bottom fifty mills of oil out of a twenty litre barrel because it was so shitty. Also, if you have shims then a change of oil or an oil additive is going to do nothing... you just need to adjust them. Adjusting shim clearances is a simple process. You measure all the clearances that you have at the moment and write them all down. Then you pull all the shims out and measure them and write that down under the first lot of figures. Now calculate how much thicker or thinner each shim needs to be to get the clearance within allowed spec. There will be two figures you come up with, one for the minimum c;earance and one for the maximun clearance. Now that you know what thickness shims you can use for each valve, go through the shims you have there and see which ones can be used where. Thnk it through and use them in the best combination possible and you may only need to buy one or two shims. Engine reconditioners or someone in the club will likel have the shim you need.. swap them for your old unneeded ones.
-
Yeah I was trying to remember why we were having trouble with yours. I reckon you are right, if we'd kept on it we would have worked it out. You sure are a persistant bugger I gotta say!! I like it. His OBD plug only has the #1 pin, so it will be subaru data I'm sure, not to the OBDii format. It did occur to me today rereading that if we had tried jumping up an Elm interface to the #1 pin that we may have got relevant data... but too late now... Anyway... Chaminda.. If you want to try and connect, and you can get what is called an ECU Id number, and it starts with 7, so somthing like 743315, then you can read all the data; log it, display it as guages. Have a look in those email meassages, check if you have the wires coming out of the correct ecu pinouts and if not then connect some. If they are there, take note of the colours and trace them or check whether they go to the OBD plug. You could also look under the dash above the knee panel to see if there is a yellow nine pin subaru diagnostic connector, some cars have the subaru connector and the OBDii connector.
-
Ok, extracts from email corospondence between Gazzy and myself... 6-12-2009 2:51 From me.. Hi again. I just realised that the possum borne pdf had pinouts in it! Doh! In the possum pdf it shows the diagnostic pins coming out of the impreza ecu as being on pins 136 3/4, so there are two of them, which means ssm. In the bh diagram there is only one wire going to the diagnostics plug so that means obd2. Since you have the impreza ecu I suspect that if you tapped straight into the ecu you would be able to read it... with ssm. That though doesn't agree with Hamish's theory that it's OBD2... confusion. I looked in your bh pdf and it doesn't show any wires coming out of 136-3/4, which it calls 52/53. If you have a look and there are no wires coming out of there then you can probably put two wires in there and get out ssm rx/tx. This is all assuming that the possum pdf is right for your version of ecu. There are different markets with different ecus which have different pin-outs and different roms in them. I presume the possum is for a N.Z, market... it is possible you have a Japanese market impreza ecu in which case we might be wrong anyway. The good news is that the ftdi cable will prevent you blowing up either the laptop or the ecu. I'd check if there are no wires in 136-3/4 and if there isn't I'd put wires in them and connect to the ftdi cable and see what I got. 6-12-2009 3:03 from Gazzy UPDATE: no pins on the BH5 blue plug where there should be, yay, that’s good. Now that we know the STI ECU is poking rx & tx out them. Now to find a way to get my wires in there……. Stay tuned……… 6-12-2009 3:52 From Gazzy.. OK, Took ECU out and soldered wires straight on to board pins. We are connected with evo scan!!!! Using Subaru and ssm1 No data showing in real time, yet ECU ID = A1100D Sound familiar Gazzy? Pretty sure that's what is going to be needed here as well...
-
Oh what! I thought you'd have the entire episode on file Gazzy! We could probably search emails and find the info? I'll have a look in my mails and see what is there..... And a happy new year to you too.. and the family.
-
If you want to get the data out of the ecu you should pick Gazzy's brains about where he connected the laptop interface wires to his ecu. Then you can use evoscan to get data out and depending on the ecu ROM number we may or may not have the addresses you need to query. It will be quite a bit of work just to find out whether you are going to get useful data out or not.
-
The data that is in there, is in different addresses for different models, so we need to know which address to query for the information we want out of each particular model car. The information we get out needs a formula applying to it to make the figure meaningful and relevant; the formlas required are different for different models as well. We can just extract all the information, and by taking repeat copies of the information while we do things to the engine, like holding the throttle down say, we can search for data that changes and figure out that that changed data is for the throttle etc. Then we have to decide upon a formula that makes that figure right for it's purpose. I have done this process before and found the correct addresses and the correct formulas. In the case of Gassy's car though.. we had great difficulty finding some of the addresses. To verify that all the addresses we have found are correct and working properly we need to compare them to other figures. So for instance, to check the knock figure we compare it to the advance and load figures as they change. If we don't get enough addresses worked out, we can't do the cross checking... which is the position we are in at the moment. Those changeover vehicles are rare in an international scale and it's not really worth doing I don't think.
-
Hi, well you don't have OBDii. So that software you were hoping to run is not going to work. In theory you should be able to get subaru specific data out of there but in practice when Gazzy tried it with me helping out over the internet we couldn't get it to work till he hotwired some wires straight into his ecu.. not sure why they was. Ask Gazzy if he still has the write-up about how and where he connected wires if you really want to do it, but, also ask him about the garbled rom addresses we experianced... lots of the data we got out was meaningless. It seems that those cars are right on the change over to OBDii and they are using odd rom addresses for the data we need for engine monitoring. It should be possible to figure out which address is which with a bit of observation and experimenting but gazzy and I didn't manage it. The system you have is Iso. Evoscan will do it as will VWRX software.
-
Hi there Chaminda. You are right, it's complicated and confusing. There are protocols/conventions for the connectors and for the communication "language", and the two sometimes get "mix and matched". I'd think that your car will be using the ssm protocol only. Later models use OBDii and SSM as well. The first thing you need to do is look for connectors. There are two types, the OBDii and the small SSM type. You may have either or both. If you have the OBDii type, it could be connected up to use the OBDii(but I doubt it in that year), or it could be using the SSM protocol still. The way to tell whether the OBDii plug is using OBDii or SSM is by checking which pins are in it and which pins are missing. So get under the dash, best to pull the cover off from under there, lay on your back and have a good look for the yellow SSM plug and for the sixteen pin OBDii plug. If you have the OBDii it would be a good idea to take a photo of it because some of the information you read on the net will be describing the pin locations as seen from the front and some as seen from the back. Best to get a photo. If you can't take a photo then make a drawing as seen from the side where you would push the test plug in from and identify which pins are there and which are missing. Post up the results and we can take it from there.
-
I'd be suspecting a sticky valve given the symptoms. If the clutchs are worn there is a lag going into gear but it is measured in seconds... not minutes. If it's taking minutes to engage gear then the clutches would be non-existant and there would be no drive! Worn clutches don't "clunk" into gear. I reckon there is some tiny speck of something(rust, metal, warpage due to loose bolts), causing a valve to stick in it's bore, then when the aluminium warms and expands after a few minutes the valve frees and moves to allow the fluid through to the clutch pack. If it isn't a sticky valve it could be the OWC slipping.. then locking up with a "clunk". Those would fit the symptoms... worn clutches dont.
-
Might be something here... http://www.cars101.com/subaru/keyless.html#97 legacy
-
P1111... aymospheric pressure sensor high? The sensor is in the ECU if it is that. It disregards the readings and fixes the atmospheric pressure at some figure.
-
Do a stall test.
-
That's the theory, in practice to find the likely addresses you can live scan in vwrx, (if the 803315 worked in evo it will work in vwrx too once you have sussed the setup), and you look for data that moves at all.. anything that changes as you change the engine parameters. So you start doing a live scan without logging and you let the motor idle say for a few minutes and look at the data, then you do something like pull a spark or injector or rev it up to double the idle revs for a few minutes and keep looking and see if you spaot what changed.. If you can't spot the changing fugure as it scans live then you will have to log, sort and inspect the data... which takes longer. I have found a few addresses using this technique in several different models. I've tried helping guys on here to find addresses too but only with limited success. It helps if you know what sort of change should happen if you change a parameter, like high O2 and increased IPW if you pull a spark, or the same O2 and increased IPW if you pull an injector, double the revs if you double the idle.. stuff like that. Try pulling an injector or something and see if the 703315 will log fault codes for that, If it does then probably all the addresses are going to be correct.
-
Ha, that's weird. 703315 is a file I made for my old 1990 non-turbo... shouldn't have all the sensors you need. Wouldn't have thought it would be the right addresses either. Basicaly what you do to find adresses is log a range of suspect or likely addresses and while they are cycling through all the addresses you wait till it's done half of them then pull a sensor and log the rest of the cycles. So you set out to log fifty addresses say and you are going to log each address ten times.. after five cyles you pull a sensor and log another five cycles through the addresses. Now clean all the text out of the log if it's a text file and paste the data in a spreadsheet, or it will already be in a spreadsheet. Choose the first colum, which is the addresses, and sort the data by that colum. You will end up with ten of the first address then ten of the next address and then ten of the next address etc. When you look at the address where the sensor is that you pulled off, it will have the first five figures then a radical jump for the next five... so the ten figures are split at the point you pulled the sensor.
-
Surging can be caused by the butterfly being adjusted incorrectly. The ISC valve needs to be in the centre of it's travel at idle speed or it takes too long to adjust a few revs, so hunts up and down always being a bit too slow to react after the motor revs have changed.. experiment a little bit at a time with the butterfly's screw. As you say though, clear the codes, go for a good drive using all revs and throttle settings etc to let it relearn.
-
Wires on the ISC are reversed? Causing it to move in the wrong direction?
-
yeah but the D/C goes high to try and keep the revs up, a blockage is the problem and a low idle is the symptom, the high D/C is the clue. You have a high idle, which may be too much air flowing through the IAC.
-
Hi, wouldn't think so... the shields are all earthed fulltime so if the other wires/sensors are using the sheilds earth as their earth it means they are meant to be earthed full time too. It could be though that the same reason he had earthed the junction block is a problem now... like a broken circuit board inside the ecu for instance, or the ecu's earth is faulty? None of those should make it rev high I don't reckon though. Is it high and steady or fluctuating? Does it vary from cold to hot? The idle control valve has a water temperature compensating bimetal spring in the bottom of it... From he manual... Idle Air Control Valve (IAC) operation controls all idle speeds. Construction includes an air cut valve, duty control valve, intake air passage and a coolant passage. These component parts create a dual control over the IAC. The air cut valve is influenced by the temperature of coolant flowing through the IAC. A bimetallic spring is utilized to act on the aircut valve, opening the valve when coolant temperature is low increasing air flow and idle speed. When coolant temperature is high the bimetallic spring closes the air cut valve and decreases airflow and idle speed. Duty control valve operation is achieved by utilizing two electrical coils, one to open the valve and the other to close it. The ECM controls the ground circuits of the two coils and controls them with a duty signal, pulsing the ground circuits. IAC duty ratio can be monitored with the select monitor. Higher duty ratio will keep the valve open longer increasing idle speed. Lower duty ratio provides lower idle speeds. Optimum idle speed for all engine conditions is part of the ECM logic and will increase or decrease IAC duty ratio as necessary to maintain the correct idle speed. IAC Schematic Fail-safe results of the IAC can be miss leading. Failure of the bimetallic spring with the aircut valve in the more open position will result in no problem with a cold engine but as the engine warms the duty ratio of the IAC will be lower than normal to close the duty control valve more to maintain proper idle speed. Failure of the bimetallic spring in the more closed position will result in higher IAC duty ratio with a cold engine but will be normal with a warm engine. Failure of the duty control valve or loss of duty signal will leave the duty control valve fully open. With a cold engine the air cut valve is also fully open. This quantity of air flowing through the intake air passage would result in an improper high idle speed. To control this condition the ECM will turn off injectors to reduce idle speed. One injector for a warm engine and two injectors for a cold engine. The intake air passage can be contaminated with carbon which reduces the air flow. This condition would result in a higher than normal IAC duty ratio. If this condition is suspected clean the IAC valve following procedures outline in the service manual.
-
Hi Gazzy, long time no see. Air leaks, aircon switch/idle up, neutral switch, alternator control can all affect idle speed. The purge should be closed at idle, they only open when warm and with a bit of throttle on. You could pinch the hore off though to make sure.
-
I'm with boostin... they are reusable. The manual says so if you read it. Do the job properly and they will be fine. When you go to do the bolts up, torque them to the first figure then put a felt tip mark on each bolt aiming forwards, it doesn't have to be precise because you are going to use your bar to measure the degrees, but it's really easy to be sure whether you have done that bolt or not... people getting confused and not doing the two ninety degree turns is the most common problem I suspect.. they either do an extra quarter turn or they don't do two.
-
Hi, I've put a new data file here ... http://cid-4ca3c3459aaa7f7f.office.live.com/browse.aspx/.Public?uc=1 The one you want is called "data of legrs", you need to rename it as data, then rename your existing data file as old, then put the new version in place of the old data file, that's in the "data settings" folder in evoscan. That will give you more models to choose from. If you are lucky either the 7136** or 7326** models will work for you, they are early model turbo'd legacies. To get the vwrx software to work you need to rename one of the existing data sets to your ecu number 703416. There is another data file for the vwrx at that same download site, it has more madels added to it as well so it might pay to download that and put it into the vwrx program using the same renameing process. Let me know how you get on and I will modify the data file again so it has your ecu number in there if you have some luck with it.
-
Evoscan will work, you just need to get the cable to connect. What sort of cable are you using? Depending on the version of evoscan you may need to choose either "subaru" or if using the older 2.5 version you need to use the OBD1 tick-box. The order of operations is, find the port number in "mycomputer", set that port number in exoscan, choose either subaru or OBG1, start scanning and see what ecu Id number you get, add or choose an adreess file that will get you the right data for that model of ecu. If you get the ecu Id number and message me I'll send you a data file that will support yor ecu... providing I have one. Have a read here and message me if you want advice... http://www.clubsub.org.nz/forum/index.php/topic,5652.0.html
-
Who's Online 0 Members, 0 Anonymous, 70 Guests (See full list)
- There are no registered users currently online